8 Types of Lathe Tooling to Get for Your Workshop
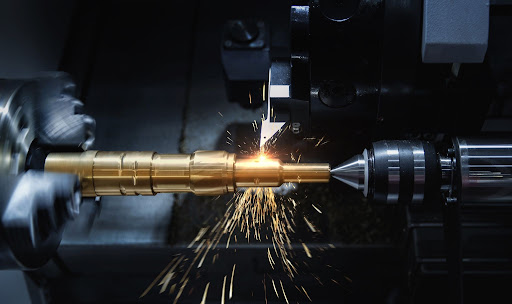
As the name implies, lathe tools are used on a lathe — a machine that rotates a workpiece on its axis against a range of different tools, typically for metalworking and metal turning.
The type of lathe tool used depends on the specific lathe operation needed, such as:
- Turning
- Grooving
- Parting
- Boring
- Drilling
- Reaming
- Threading
Lathe machining is a complex subject, and any decent machinist will tell you that you can write books about different aspects of lathe work.
In this guide, we’ll try our best to condense everything you need to know about the different types of lathe tooling by their use in your average machine shop.
1. Turning Tools
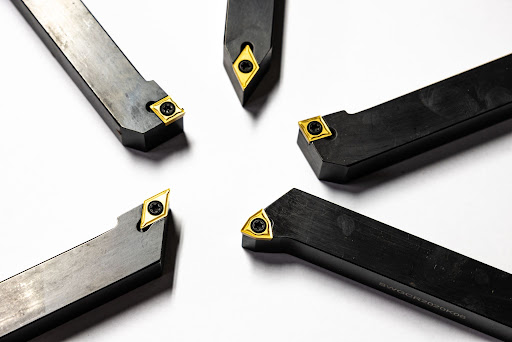
Turning is the process of using a single-point turning tool and moving it along the side of a workpiece (axially) to remove material and create different features, such as contours, tapers and steps.
Turning operations use a wide range of turning tools that share similar features:
- A replaceable turning insert: This serves as the tool’s cutting edge. Inserts come in a wide range of shapes, dimensions and tolerance, each ideal for specific turning applications.
- A turning tool holder: The body holds the insert and is mounted on the lathe turret.
2. Boring Bars
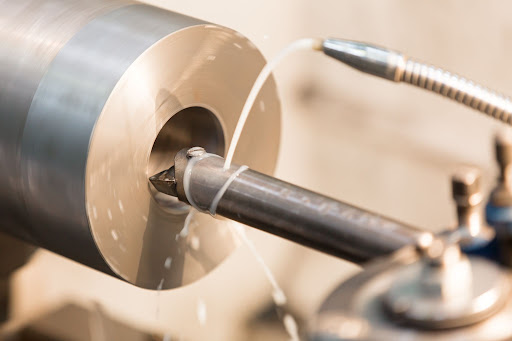
Boring is an internal operation that involves cutting into the workpiece axially and removing material from its inner surface. You can use this operation to produce cylindrical or conical features inside a workpiece, typically to enlarge an existing hole or opening.
For instance, if a workpiece with an existing hole needs to accommodate a larger screw, you can use a boring bar to widen that hole’s diameter to precise dimensions. You can also leave behind a rough bore for threading.
3. Parting and Grooving Tools
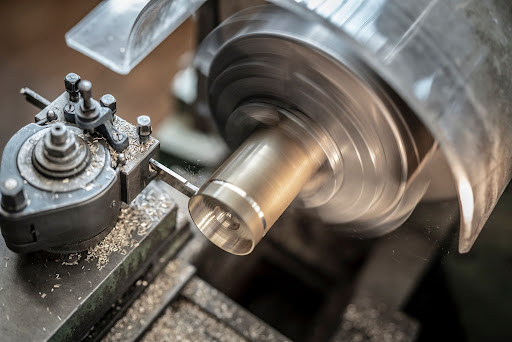
Parting and grooving are related lathe operations with slightly different results.
Parting is a lathe operation that involves using a blade-like cutting tool to cut off sections of a workpiece at a specific length — hence the term “parting”. In most parting operations, a parting tool (also known as a parting off tool) is used to make very thin and deep cuts into a round bar.
There are two primary cutting tools for parting off operations on a lathe:
- High-speed steel (HSS) parting off blades
- Carbide parting off inserts
Other non-cutting tools for parting off work include parting blocks and wrenches.
But what about grooving?
Grooving is a very similar machining operation, except that the cuts you make are shallower and don’t reach the middle of the workpiece. In other words, you’re using a cutting tool to leave grooves. These can vary in width, depending on the features you want to create on a workpiece.
4. Chamfering Tools
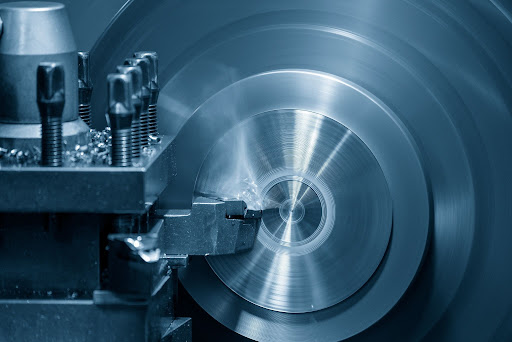
A chamfer is a sloped or angled edge or corner, often serving as a transitional edge between two faces of an object. A chamfer can also be a safety feature, smoothing sharp edges on a workpiece to make it less hazardous and less susceptible to taking damage.
Many machine shops use straight turning tools as an improvised chamfering tool — simply set the cutting edge to your chamfer’s desired angle. However, if you intend to perform a large number of chamfering operations, you can use specialised chamfering tools where side cutting edges are ground to the angle of your chamfer.
5. Knurling Tools
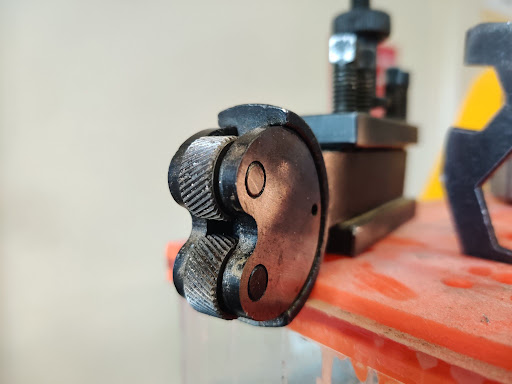
Knurling is a machining process of creating knurls on the surface of a workpiece.
Knurls are small ridges, often in square or diamond patterns, that give the lathed part a rougher finish for better grip — ideal for machining knobs, fasteners and handles. Knurls are also used to repair or hide wear on a machined part.
Knurl patterns to choose from include:
- Diamond or checkered knurl
- Straight knurl
- Left-hand and right-hand knurl
These patterns also come in coarse, medium, and fine texture variations.
Whatever the case, knurling tools will have a set of steel rollers mounted on a tool holder. Knurling tools create patterns by either cutting into the workpiece and removing material or leaving impressions in a non-cutting process known as form knurling.
6. Thread Cutting Tools
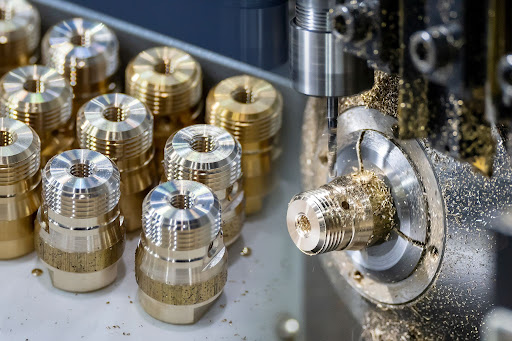
Helical grooves or threads are created by thread cutting tools on a workpiece in two ways:
- External (male) thread cutting: The work piece part is held by a chuck or two lathe centres. This operation requires a turning point moving axially along the side of the workpiece, cutting threads into its exterior surface.
- Internal (internal) thread cutting: The workpiece is held in a chuck, and the tool makes cuts to its interior surface. You can use turning inserts and boring-type tools for this operation.
7. Facing Tools
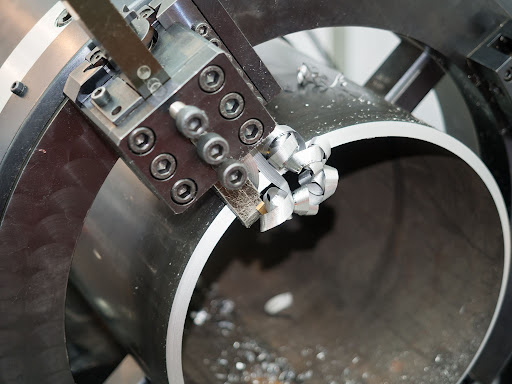
Facing tools are essentially turning tools. But unlike turning, facing involves moving a single-point tool along the end of a workpiece radially. This process removes a thin layer of material from the workpiece, leaving behind a very smooth finish.
Because the depth of the cut tends to be very small, you can complete the facing process in a single pass. Alternatively, you can machine at an even smaller cut depth and make multiple axial passes for more precision.
8. Forming Tools
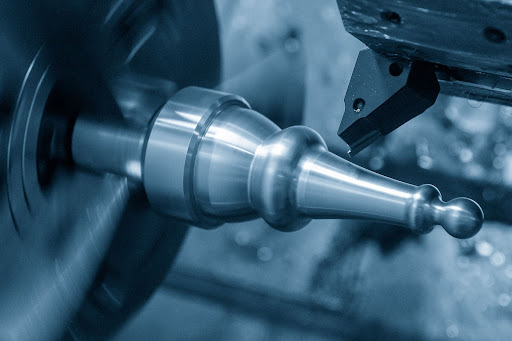
Forming, or form turning, is a machining operation for creating a convex, concave or any irregular shape on a workpiece.
Forming tools (or form tools) are not designed to remove large quantities of material from a workpiece and are instead used for finishing already-formed surfaces. Machinists typically use two types of forming tools:
- Straight forming tools: These are used for wider surfaces
- Circular forming tools: Their circular profile is ideal for narrow surfaces
Follow the Milo Tools blog to find more advice and expert tips on lathe tools and other precision cutting equipment. If your business or shop needs help deciding what tools to use for a specific job, get in touch with one of our time-served engineers and get FREE expert advice.
You can also explore our extensive collection of lathe tools, including ISO turning inserts and tool holders and parting and grooving systems.